
Thu September 20, 2018
Eric Olson –CEG Correspondent
No matter their size or configuration, off-road haul trucks would have to be considered as the “strong men” on any construction site or quarry.
Whether they are big, rigid haulers (off-roads with conventional front steering and rear-wheel drive), articulated haulers (more maneuverable trucks with a tractor and a trailer section) or compact dumpers, these burly machines are designed to carry heavy loads of dirt and rock in and out of a work area.
You see them on practically every project that requires earthmoving and clearing, as well as at mining operations and timber hauling jobs. Off-road haulers also can be used in many military operations.
Beyond their basic forms, though, there are differences between articulated dump trucks (ADTs or artics) and rigid haulers. Both are ruggedly-built, but the lighter frames of ADTs allow them to adroitly haul material over rough terrain, as well as skillfully handle great inclines and slippery conditions. Rigid haulers, though, excel with a higher load capacity and have become the preferred machine for use in moving more rock, dirt and sand from mines and quarries.
When choosing between rigid haulers and ADTs, a contractor must factor in the material, the road conditions, what loading tool the hauler will be paired with, how much production is needed each day and how long the project is expected to last.
Working Conditions Dictate Use
The differences between each vehicle also helps determine how they are used, the most common of which are the conditions of the construction project where they operate.

“An ADT is the preferred method to haul materials anytime a company is working in an off-road situation such as an 'open' job site,” explained Aaron Kleingartner, marketing manager of Doosan Infracore North America, which currently offers a pair of heavy-duty articulated trucks in its lineup. “ADTs have better capability to easily traverse muddy or soft terrain with six wheels, as opposed to four on a rigid dump truck. Six wheels also spread out the articulated dump truck's load over a larger area.”
Because ADTs have better maneuverability, they are well suited to small sites, as well. Articulated steering improves mobility in confined areas where a smaller turning radius is an issue.
“Many operators want to stay within a narrow path or area when working versus making wide turns on the surface each time the truck is loaded and carries material from point A to point B,” he continued. “As a result, ADTs are the most common truck used on off-road construction job sites in the United States and Canada.”
Doosan's ADTs feature a tandem bogie function that helps keep its tires in continuous contact with the surface for improved traction, stability and safety, Kleingartner said.
Besides the number of wheels found on ADTs, Doosan's oscillating and articulating hitch allows the trucks to work in extreme conditions. They haul well on grades up to 35 percent, rolling resistances of 20 percent and with loaded haul distances from 500 to 10,000 ft.
Even though mines and quarries have historically been the exclusive home to rigid off-road trucks, ADTs are now being made to carry larger loads within those applications to remove overburden.
Other job sites where ADTs are effective are road building, site preparation, reclamation projects, and transporting fly ash at coal-burning power generation facilities. Contractors also are using them on subdivision construction, retention ponds, hydroelectric dams and even canal building and expansions.
Rigid Trucks Are the Big Guys
That is not to say that rigid dump trucks have been forced to the sidelines. These veteran machines were in use before the invention of ADTs in the 1950s and, today, their size and hauling production is vital to many types of construction, mining and forestry work.
Rigids haulers also are typically much bigger than their teammates on a construction project (not counting heavy cranes) — akin to a nose tackle on a football field, albeit on a much larger scale. These squat machines can carry larger loads than articulated dump trucks, but their weight requires an improved surface on which to travel.
They're the best choice for applications with few roads and long travel distances, when a large volume of materials needs to be moved or quick load times are required. Those conditions are typically found in surface mines or large sand, gravel or rock quarries, where road surfaces have generally been established and maintained for years.

Caterpillar manufactures six rigid haul trucks for construction and another eight for mining purposes, besides a line of seven three-axle ADTs.
Its popular 770G rigid hauler has a maximum payload class of 46 tons and is a beast on construction and mining sites.
“We are always designing all of our off-road trucks to improve efficiency,” said Mike Mesnard, a product application specialist of Cat haulers. “This allows customers to improve cost-per-ton on a per-unit basis. We do this through efficient machine weight to horsepower improvements while maintaining durability standards and improving fuel consumption.”
Rigid off-road trucks are heavy rear-wheel-drive machines, meaning they typically perform best on grades of 10 to 15 percent or less.
But, where rigid off-road trucks have their clear advantage over ADTs is in their payload capacity.
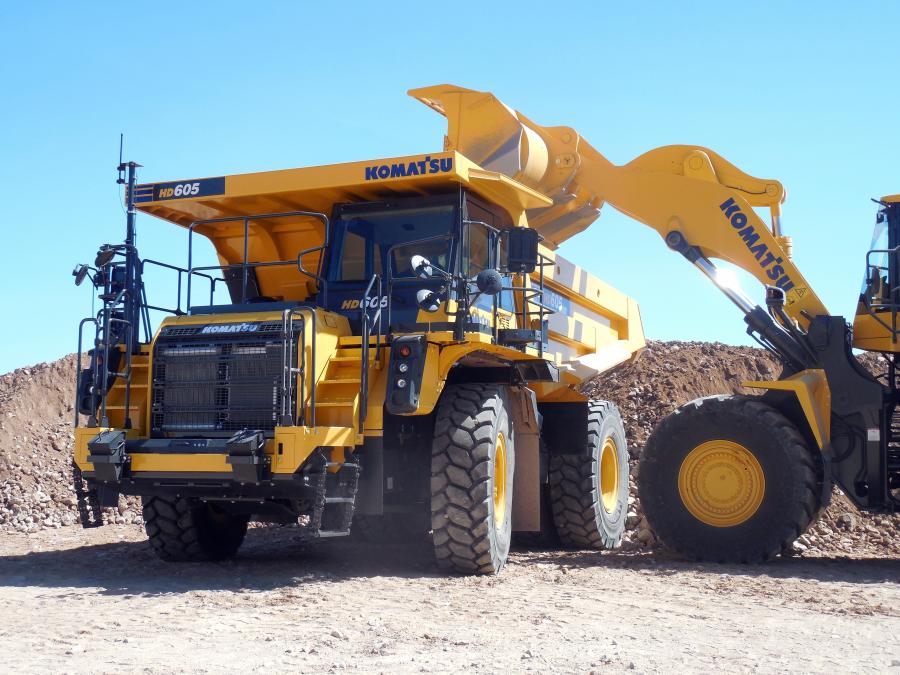
As an example, Komatsu's six mechanical truck models haul between 40 and 158.9 tons, compared to its pair of articulated trucks, with capacities of 30.9 and 44.1 tons. The manufacturer also offers a line of seven electric-drive, rigid dump trucks ranging from 200 to 360 tons.
Other makers of full-sized rigid off-road trucks have similar load capacities.
“These rear-wheel-drive trucks are capable of longer hauling distances at higher speeds that put too much wear and tear on an ADT,” said Maryanne Graves, John Deere's product marketing manager of ADTs. “When factoring in which type of truck to use, it's first and foremost all about the site and the project itself. The amount of material is secondary.”
Increasingly, though, it appears the versatility and adaptability of ADTs has created a popularity race with rigid off-road trucks in the eyes of contractors and dealers. Regardless, improvements are constantly being studied and implemented on both types of road-trucks to boost performance and safety.
Volvo: A World Leader in Off-Roads
Volvo has long been recognized as a pioneer in the development of ADTs and just last year built its 75,000th artic truck. The company has produced more than half of all ADTs ever made, with two thirds of its models still in regular use around the world.
Unlike many manufacturers, though it also builds a line of both ADTs and rigid trucks.
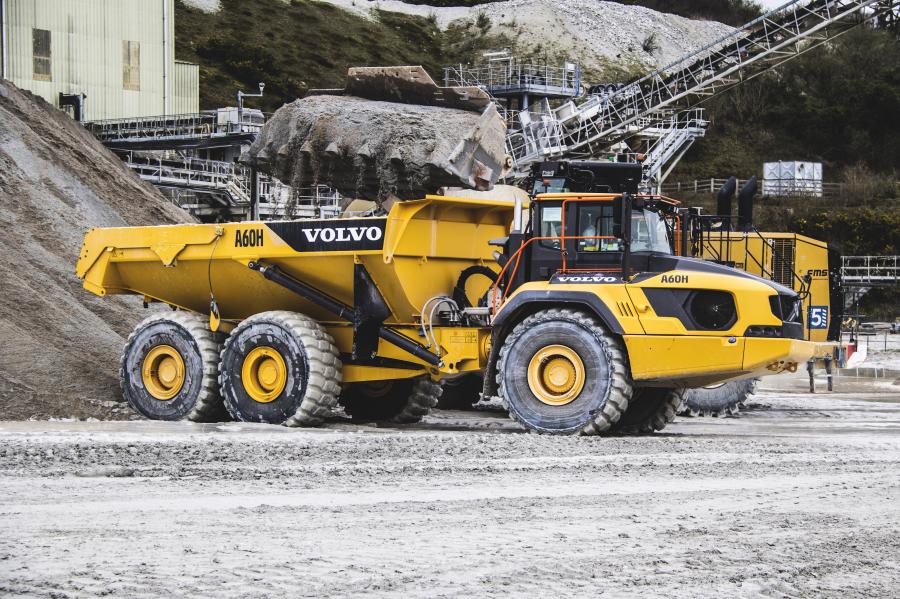
Rob Palermo, ADT product manager of Volvo Construction Equipment, explained that his company has been able to boost the capacity of its ADTs, exemplified by the model A60H, the largest artic on the market. The vehicle offers a 60-ton payload capacity, matching the capacity of some smaller rigid hauler models, but with the ability to go where rigids cannot.
“Outside of the A60H, we also made payload capacity increases across a number of our G-Series models in 2017,” he said. “The three smallest of the G-Series haulers now have a 1-ton-higher capacity than before, including the Volvo A25G at 27.5 tons, the A30G at 32 tons and the A35G at 38 tons.”
The bigger G-Series trucks are the A40G, with a capacity of 43 tons, while the new A45G/A45G FS models have a 45-ton capacity.
In addition to payload capacity increases, other improvements by Volvo were aimed at making the machines more efficient, safe and productive. For instance, Volvo's On-Board Weighing feature now comes standard on the A35G, A40G, A45G and A60H models, and is an option for the A25G and A30G.
“The operator can see the actual tonnage in real time,” Palermo said. “Three load indicator lights alert both the hauler operator and the excavator/wheel-loader operator when the correct load has been reached. This saves everyone time and increases their productivity.”
Volvo's recent generation of ADTs began using Hill Assist, which holds the hauler in place on steep slopes without the need to engage the parking brake. The feature automatically activates when arriving at a complete stop on a hill and is disengaged when the operator accelerates.

Palermo also pointed to Volvo's recent advancements aimed at assisting operators to better steer both its rigid haulers and articulated trucks.
“Our hydro-mechanical steering system lets an operator precisely control the machine and creates a short turning radius,” he revealed. “Steering can, of course, be difficult if you also have to concentrate on choosing the optimal drive combination. Volvo's Automatic Traction Control lets operators focus on driving while automatically engaging and disengaging locks for the most efficient on and off-road performance.”
He described Volvo's engine brake as “one that uses powerful retarders to control speed while hauling downhill to slow down before curbs or crossroads.”
The company's ADT also comes equipped with full wet disc brakes on all wheels, ensuring high braking performance and long service life for machines regularly working dusty and muddy sites.
Bell Trucks Go All-In with ADTs
Based outside Charlotte, N.C., Bell Equipment has chosen to manufacture only ADTs, with 10 models from which to choose. The company's Kevin O'Donnell was recently asked if upgrades to both types of off-road trucks are engineered to specifically improve capacity and overall sophistication.
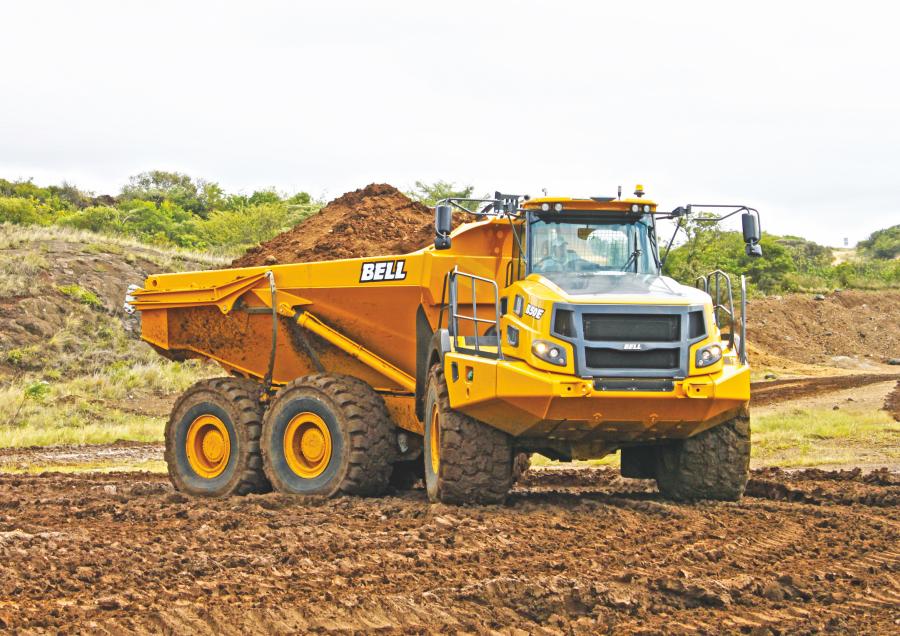
“Our opinion is that payloads won't increase much in the short- and medium-term to increase production,” he replied. “But, as the offerings to the marketplace have changed significantly in the last few years, customers need to assess what machines are the right size for them.
“This is not a simple process as the selection of ADTs, for instance, can affect the other machinery on the job site, which are generally on a different replacement cycle. The drive for lowering the cost per ton of material moved will always be there and larger payloads are an effective way of achieving this.”
O'Donnell also explained that engineers are adding to an ADT's sophistication as an “unintended consequence” of making them safer to operate, more driver-friendly, more fuel-efficient and more productive.
“Upgrades are an evolution that happen over time to the demands of regulations, customer requirements, work conditions, etc,” he said. “Trucks working on a site that has overhead power lines, for example, require engineering to develop a feature that will not allow their bins to raise if under a utility line.”
Customers Help John Deere Make Upgrades
John Deere produces five ADT models, with rated payloads from 53,000 to 92,000 lbs. The upgrades to its machines are often due to the company's heavy emphasis on responding to feedback from dealers and end-users of its products, said Maryann Graves.

“I don't think any customer would not tell a manufacturer that they don't need to improve fuel efficiency,” Graves said, “and we do look at that, but there are other things our customers are happy about, such as our adaptive suspension. But, they do ask for increased safety features all the time — 'How can you help us protect our people and my investment in the truck?' I think we already do that better than anyone else in the business, but we are constantly looking to improve.”
She also cited John Deere's ground-level daily service as being an asset to owners and operators, where every routine pre-use check on its trucks can be done with the person's feet planted on the ground.
“On our ADTs, the operator can walk up to the truck, check all the daily maintenance items, such as grease points and fluid checks, then get in the truck and go,” she said. “There is no climbing up and opening the hood or something similar. It can all be done from the ground and that is an important safety feature on our ADTs because many of them are used on soft ground or on inclines.”

Another of John Deere's operational safety features is its rollover protection. This function allows ADT operators to set an incline percentage in the monitor. When their truck is above that percentage, the monitor will stop the operator from dumping the load. The technology does so after determining that the artic is not on a safe slope and that the operator has to re-position the truck before trying again.
Graves added that if you can drive a car, you can drive one of John Deere's ADTs. They may be sophisticated in their design and engineering, but a contractor's newest people can quickly learn how to use them.
“I had a customer, the owner of a large operation, tell me once that 'it is very ironic that you take the least experienced person and put them in your most expensive piece of equipment', but we know that and keep working to make them simple to operate,” she said.
Komatsu Has Whatever Truck You Need
Unlike many other manufacturers, Komatsu has focused more on rigid off-road trucks with a total of 12 (six mechanical and six electrical models) in its product lineup, along with two ADTs.

Komatsu's HD325-8 mechanical truck is a perfect example of the kind of design and engineering needed to compete with similarly-sized ADTs. Although it has the smallest load capacity of the maker's rigid haulers, the hauler is a 40.3-ton-capacity workhorse. It is very maneuverable and its MacPherson-strut-type front suspension gives it the tightest turning radius in its class.
With two working modes, the operator can most effectively take advantage of the fully-automatic seven-speed transmission with lock-up feature. A hydro-pneumatic suspension also gives the operator a comfortable ride while maintaining more material in the bed, giving him more production. It also gives the truck a wide, stable stance, resulting in a higher steering angle.
The HD325-8 machine also benefits from Komatsu Traction Control (KTCS), a standard for optimum traction in all ground conditions.
The manufacturer is betting that its rigid off-road haul trucks will continue to evolve and thrive in the marketplace, according to Frank Nyquist, marketing manager of quarry products at Komatsu.
“Rigid-frame trucks already occupy such a wide range of capacities,” he said. “If larger tools are constructed, then the size of these trucks will surely follow. Transportation and tire capacities are just some of the parameters that will dictate the effective sizes of ADTs.”
Look for More Upgrades to Come
Regardless of their frame configurations, a host of improvements will continue to be designed and made by each of the manufacturers of off-road trucks.
Kevin O'Donnell of Bell Equipment said the focus for all OEMs is the upcoming Stage 5 emissions regulations in Europe. While the U.S. Environmental Protection Agency (EPA) does not have any immediate plans to introduce equivalent regulations in this country, that OEM development work is still required.
“One of the benefits of Bell Equipment trucks in North America is that our Tier 4 Final solution from Mercedes-Benz do not require an expensive DPF [diesel particulate filter] and the maintenance issues that go with it,” he said.
Software features on ADTs become more sophisticated each year, as they do on all construction equipment.
O'Donnell considers Bell to be the market leader in software control for these vehicles.
“Our software gives owners and operators flexibility in adjusting how a function on the ADT behaves,” he continued. “Bell has a number of features that enhance productivity, site and operator safety and ease of operation. Software features include automated tipping and bin rollover prevention, auto horn alerts, hill-descent control and automatic traction control. Our driver ID allows the truck to be programmed with up to six different drivers, each starting the keyless vehicle with their own ID code that is recorded on Bell's Fleetmatic system.”

Also included on that list by O'Donnell is a turbo spin-down feature on the Bell ADT engines. When the operator pushes the shutdown button, the truck will continue to run, and then shut down, allowing the turbo to slow before the oil supply is cut. The auto park brake is automatically applied when the truck is put into neutral.
At Doosan, Aaron Kleingartner touted the fact that updates to the maker's ADTs provide lower operating costs for owners by having fewer service points with fewer oil types in the driveline and increased intervals for transmission oil changes.
“A new cab-tilting system enables service technicians to lift and close the cab in just a few minutes,” he said. “The truck is no longer built with rubber springs in the suspension, and there are only four rubber components in the entire front and rear suspension. A new air filter bracket also makes it easier for operators and service technicians to access the engine compartment for simplified maintenance.”
In addition, Doosan promotes its trucks as being among the most fuel-efficient in the industry.
Kleingartner explained that the off-road haulers in its model line combine a Scania diesel engine and a ZF transmission, improving the transfer of power from the engine to the wheels for outstanding traction. Coupled with the enhanced rear-differential system, which reduces engine rpm and further increases machine durability, customers are ensured an improved cost-per-ton carried with the Doosan ADTs.
“The demand from our customers is to achieve a hauling system where the operator can either be removed from the truck to operate remotely or provide a fully autonomous truck,” said Caterpillar's Mike Mesnard. “We see this as the direction in which the industry is heading.”
The science and sophistication that goes into how these machines are designed, whether you are thinking of getting an ADT or a rigid hauler, is truly amazing and should be food for thought the next time you are shopping for one.
CEG
Tighter Work Spaces No Sweat for Compact Off-Road Trucks

What about those job sites that are too small and narrow for the full-size off-road trucks to efficiently operate?
It certainly is good news for contractors that, increasingly, those types of construction projects are becoming prevalent, particularly in urban areas. Even the smallest full-size ADT cannot get into tighter areas without problems.
But when they cannot, builders turn to more compact carriers and dumpers to fulfill their needs.
Several manufacturers have seen success with these products, but great examples of the versatility of these machines can be found in the line of products built by Terramac and Fiori, the latter being a new entry to the American market and built by an Italian company.
Terramac utilizes a rubber-tracked system on its carriers, with Fiori choosing to employ wheeled dumpers.
Each can be found on a multitude of different construction sites performing an array of tasks, such as earth moving, hauling and clearing construction debris. Beyond that, they work effectively on environmental and utility projects, in addition to work at pipelines, landfills and mining operations.
Terramac's personnel carriers are also expert in moving crew members to hard-to reach job sites, as well. Muddy ground, steep hillsides and rock areas can all be traversed with these machines.
Terramac Tackles Problematic Job Sites
The Illinois manufacturer specializes in offering customers a line of four rubber-tracked crawler carriers, in a variety of sizes to accommodate problematic construction sites. With a load capacity from 12,000 to 28,000 lbs., they are, from smallest to largest, the Terramac RT6, the RT9 carrier, the RT14 carrier and the RT14R rotating crawler carrier.

“When large off-road trucks can't operate because the ground conditions are too soft, our units keep working,” explained Monica Coenen, marketing manager of Terramac. “The low ground pressure — 5.3-psi to 8.3-psi — and flotation of the rubber tracks allows them to run across wet, rough and steep terrain all while minimizing ground disturbance.”
The chassis design on Terramac carriers also allows a simplistic approach for interchanging bed designs and construction specific-support equipment without permanently modifying the carrier's structure.
“These vehicles are quite well-suited for jobsite flexibility,” Coenen stressed. “Besides being a personnel carrier, they can lift materials with a crane or restore the land with a hydroseeding unit, making them ideal choices.”
When working in confined spaces contractors have come to depend on rubber-tracked units with 360-degree rotation to haul materials in and out of the job site.
That is certainly clear from watching Terramac's carriers in action.

The maker's RT6, has a proven track record of working in tighter spaces due to its diminutive size, at just over 8-ft.-wide. The zero-turn radius also contributes to its nimbleness.
The larger RT14R features an upper frame that rotates 360 degrees allowing the unit to offload materials at any angle — an advantage for tight job sites. When space doesn't allow for a vehicle to make a full turn the operator simply changes the direction of the upper frame (cab and bed) and drives straight out.
Equipment With an Italian Flair
Fiori's compact dumpers are exclusively sold in the United States by Dominion Equipment Parts in Ashland, Va. The Italian maker offers three models for American customers: the articulated D40, and the larger, rigid-framed D70 SW and D100 SW haul trucks, all introduced just last year.
The first of Fiori's products to emigrate across the Atlantic was the Fiori D40 artic, the most compact vehicle in its class, providing 180-degree bed rotation and three-way dumping in a package that is just more than 13 ft. long. It has a carrying capacity of 8,800 lbs.
Specifically engineered to maneuver within tight spaces and work areas with restricted access, the machine utilizes a 49-hp Yanmar diesel engine and four-wheel-drive hydrostatic transmission to drive its articulated frame.
The bed rotation and three-way dumping allows the operator to put the load precisely where it needs to be. The dumper can be used for a wide variety of loads, including dirt, debris, or even for pouring concrete.
The truck's initial development and use in old European cities with narrow streets translates well to today's American urban building.
“The D40, like all of Fiori's trucks, works great in old sections of cities with narrow streets and sidewalks, cemeteries, path and trail building, narrow access roads and many similar applications,” explained Curt Unger, vice president of sales of Dominion.

The larger capacity models — Fiori's D70 SW (with a payload of 15,400 lbs.) and D100 SW (22,000 lbs.) trucks — each sport a tipper body and swivel bed with 180-degree, trilateral dumping ability. These robust, straight-framed carriers have four-wheel steering. Their unique truck design is a speedy and lightweight alternative to tracked carriers for jobs that make a wheeled off-road machine preferable.
“Other brands of large, off-road trucks all use articulated steering,” Unger continued. “Fiori developed its D70 and D100 with four-wheel steer and crab steering. This allows Fiori's units to be built as a rigid truck with no center pin for articulation, giving the frame more strength. Its trucks can carry a larger load on a smaller frame so access to tight and small job sites is more accessible and the units are more productive while still maintaining the maneuverability of an artic truck.”
With hydraulic components on all off-roads improving by leaps and bounds in recent years, these vehicles have become smoother and easier to use. Fiori's incorporation of the newest systems into its line of trucks has certainly been a benefit to its customers.
“The hydrostatic transmission has made Fiori operators more efficient because of less clutching and shifting,” Unger said. “They can now transition from forward to reverse and reverse to forward much faster than in the past. The trucks are much less jerky in the transmission than in the past, meaning the operator is more efficient and doesn't tire as quickly.”
Safety and Production are Paramount
Like any construction equipment manufacturer, both Terramac and Fiori develop new features and upgrades to their vehicles to increase their production and make them safer to use.
For instance, with Fiori's swivel seat recently added to the operator area for all three of its compact dumpers, the operator can travel in either direction while looking forward. The result is in tight spaces the operator can exit in the same tracks he or she entered on without having to turn the truck around or back up — an obvious safety benefit.
Terramac, too, has upgraded its operator performance and safety on its trucks by including large windows with unobstructed views on each side of its cabs, along with large mirrors and back-up cameras to improve visibility.
“The 360-degree rotation of the RT14R, for example, allows the operator the ability to always work in a face-forward position, which is an incredible safety feature,” Coenen said.
This story also appears on Construction Equipment Guide.